Ganz schön schweißreibend
WirtschaftsförderungHaag Industrietechnik baut neue Reibschweißanlage
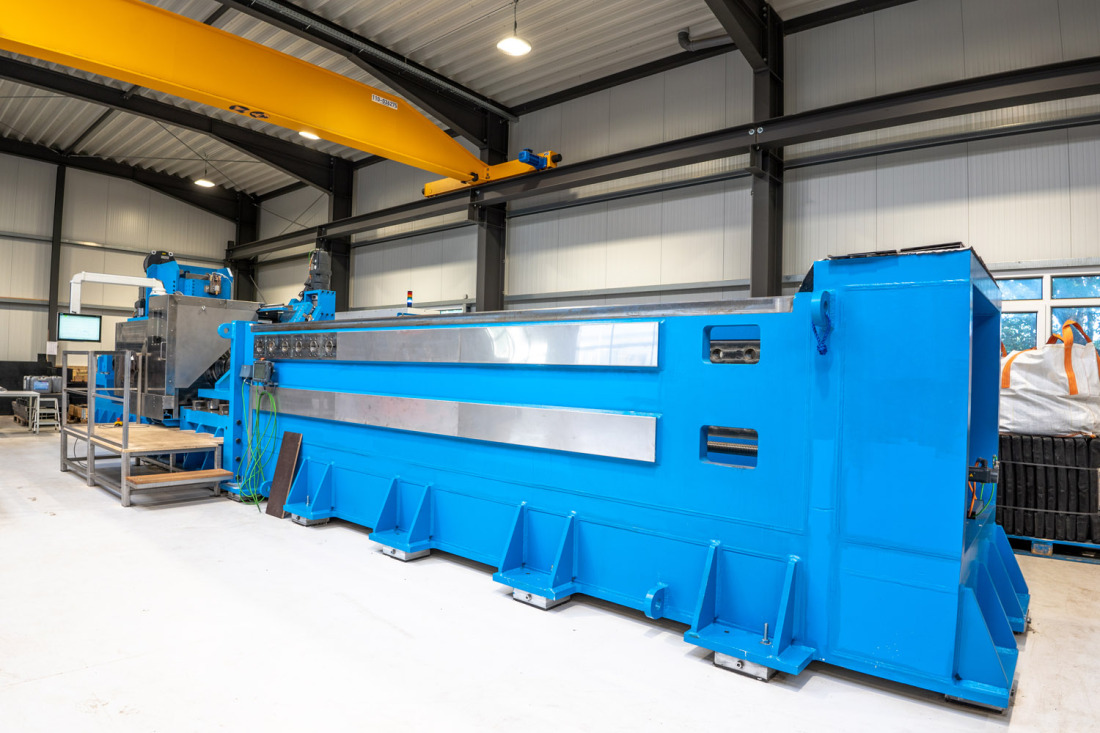
Beim Reibschweißen werden zwei Werkstücke unter axialem Druck aneinander gerieben. Durch die Kombination aus entstehender Wärme und Druck ist es nach dem schnellen Abbremsen möglich, die Oberflächen zu verschweißen. Das Verfahren erlaubt die Verbindung unterschiedlicher Materialien, wie etwa Kupfer und Stahl, führt gegenüber anderer Schweißverfahren aber ein Nischendasein. Mit einer neu entwickelten Reibschweißanlage will die HAAG Industrietechnik sich neue Möglichkeiten eröffnen und gleichzeitig Nachteile des Systems ausmerzen.
Erste Bestrebungen, eine solche Maschine zu konstruieren, gehen auf das Jahr 2005 zurück. Firmengründer Werner Haag hatte es sich zum Ziel gesetzt, beim Reibschweißen ganz auf Hydraulik zu verzichten. Denn bei herkömmlichen Anlagen wird der hohe Druck, mit dem die Werkstücke aneinandergepresst werden, mittels energieintensiven Hydrauliksystemen erzeugt. Haags Idee: Alles, was sich bewegt, soll durch Elektromotoren mit Getrieben und Spindeln angetrieben werden. Dadurch wird nur dann Energie benötigt, wenn der Antrieb läuft. Gleichzeitig fallen Ölpflege, Ölkühlung, Lekagen und der ständige Pumpenbetrieb weg. Somit steigt die Effizienz des Systems und Kosten können eingespart werden.
Reibschweißen – etablierte Technologie mit Nischendasein
Die Realisierung erwies sich als eine Herausforderung. Aus ersten Ideen entstanden 2012 in einem Förderprojekt zusammen mit universitären Partnern Ansätze zu einer Maschine, die Haag in den folgenden Jahren mit eigenen Mitteln weiterverfolgte.
Die neue Reibschweißanlage ist das Resultat dieser Entwicklung sowie langjähriger praktischer Erfahrungen des Unternehmens. Durch die Bearbeitung von Aufträgen mit kleineren, selbst angepassten Reibschweißmaschinen, sammelte HAAG Industrietechnik-Praxiswissen, das in die neue Anlage einfloss.
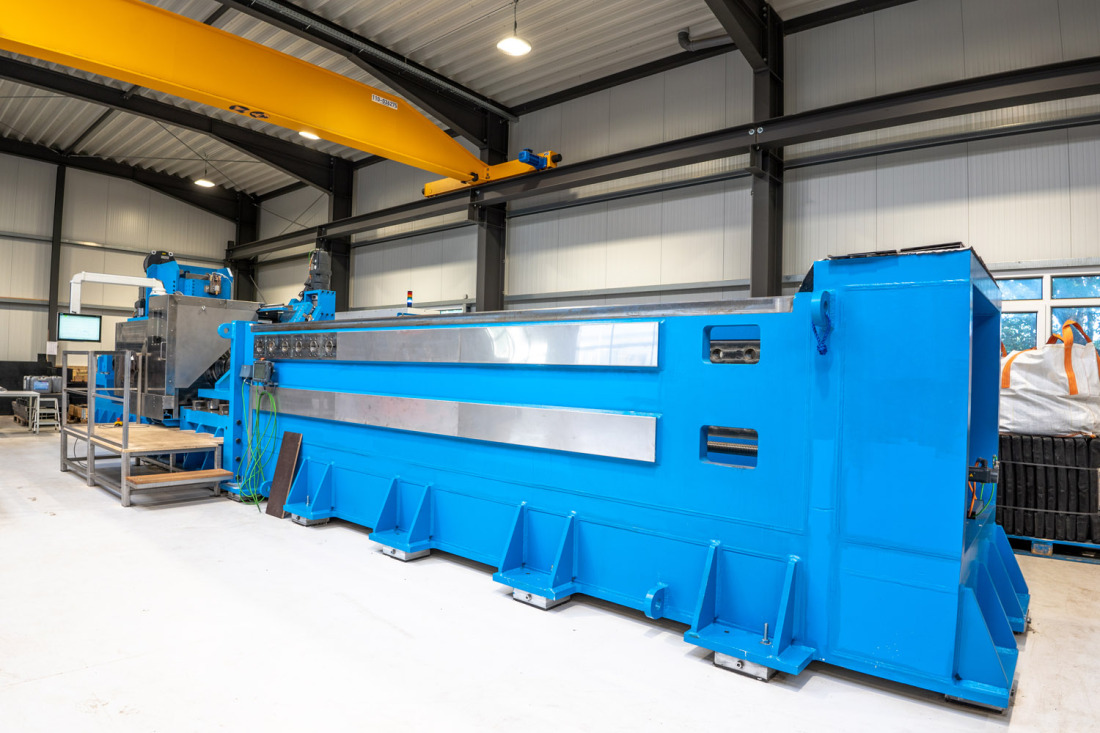
„Es gab immer wieder Anfragen zum Reibschweißen, für deren Bearbeitung unsere bestehende Maschine zu klein oder zu schwach war. Auch die Erfassung von Parametern und Daten während des Prozesses war nur eingeschränkt möglich. Aus all diesen Eingaben konnten wir Forderungen zusammenstellen, die von der neuen Maschine erfüllt werden sollten“, erklärt Werner Haag.
Neue Dimension im Reibschweißen erreicht
Eine der Forderungen betraf die verarbeitbaren Längen der Werkstücke. Die neue Anlage kann nun Werkstücke bis sechs Meter Länge auf der stehenden und zwei Meter Länge auf der rotierenden Seite aufnehmen und miteinander verbinden. Dank einer modularen Bauweise können künftige Anlagen zudem noch größer sein. Mit Durchmessern bis 100 mm kann die Maschine Bauteile mit mehreren Tonnen Gewicht miteinander verbinden – was den Einbau eines Hallenkrans bei Haag Industrietechnik erforderte.
Trotz ihrer großen Abmessungen sollte die erreichbare Präzision nicht leiden – darauf legte Firmengründer Werner Haag wert.
„Reibschweißen ist ein schneller Prozess mit inhomogener Erwärmung und elastisch-plastischen Verformungen – die Ansprüche sind also hoch. Durch die Verwendung von Servomotoren, Getrieben und Spindeln statt Hydraulik können wir viele einzelne Parameter während des Reibschweißens messen – und damit letztendlich auch präzise steuern. Das ist mit anderen Anlagen so nicht möglich“, erklärt er. „Die aufgebrachte Kraft wird nicht über Öldruck und Zylindergröße berechnet, sondern mit Kraftmessdosen direkt gemessen. Auch das Drehmoment, durch den 150-Kilowatt-Hauptmotor aufgebracht, wird während des Prozesses aufgezeichnet. Damit ist erstmals auch möglich, die sich während der Bearbeitung verändernden Reibmomente in weitere Überlegungen einzubeziehen.“
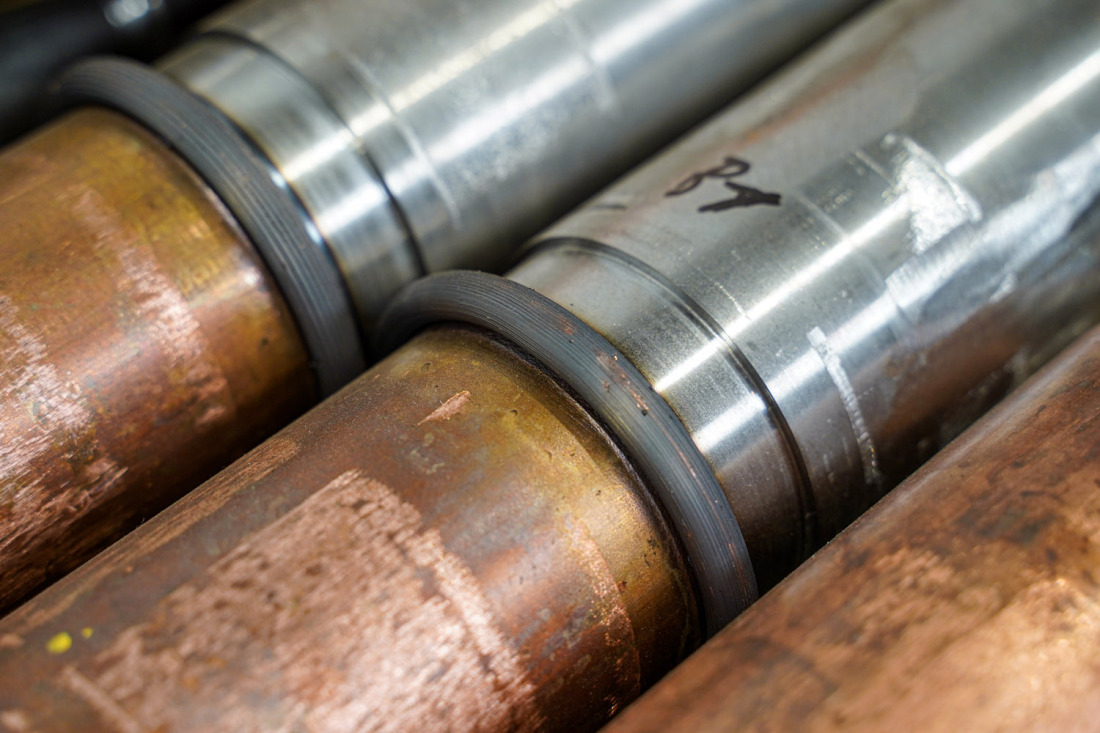
Eine eigens geschriebene Software zeichnet Daten während des Reibschweißvorgangs auf und ermöglicht es so, neue Erkenntnisse über das Verfahren und den Betrieb der Maschine zu sammeln.
„Wir haben natürlich ein großes ingenieurtechnisches Interesse daran, die Maschine genauer zu erforschen und ihre Möglichkeiten auszureizen, allerdings gibt es bereits reichlich Anfragen und Aufträge. Hier muss unsere Neugier erstmal den unternehmerischen Erfordernissen nachstehen“, so Haag.
Bisher haben sich die eigenen Mitarbeiter an der Maschine eingearbeitet und erledigen die anstehenden Projekte. Wenn es gelinge, mehr Projekte als Lohnfertiger zu bekommen, müssen wohl weitere angeworben werden, wünscht sich Haag.
Auf sichere Bank gesetzt
Stets an der Seite der HAAG Industrietechnik begleitete die BAB – die Förderbank die Neuentwicklung. Für die Maschine selbst erhielt das Unternehmen aus dem Bremer Industrie-Park Fördermittel aus dem FEI-Programm, das Innovationen unterstützt und somit Geschäftsrisiken abmildert. Zudem unterstützte die BAB bei der Erweiterung der Halle und beim Bau der Anlage mit Mitteln aus dem Landesinvestitionsförderprogramm LIP sowie mit Beteiligungskapital. „Für ein kleines Unternehmen wie die HAAG Industrietechnik stellt die Entwicklung einer solchen Großanlage ein enormes Risiko dar. Aber es bietet auch eine Chance, einen entscheidenden Schritt zu gehen und die eigene Geschäftstätigkeit zu erweitern. Wir freuen uns, dass wir hier als Förderbank das Unternehmen begleiten konnten. So erhalten wir die Innovationskraft Bremens“, erklärt Silke Muhle, Kundenbetreuerin Firmen- und Geschäftskunden von der BAB.
Auch Werner Haag ist froh über die Unterstützung. „Alleine hätten unsere Mittel nicht gereicht, um die Entwicklung zu finalisieren. Ich freue mich, dass wir hier in Bremen so einen guten Partner haben.“
Erfolgsgeschichten
Neue Finanzierungsmöglichkeit für Startups und innovative KMU
Mehr Wachstum für Startups sowie kleine und mittlere Unternehmen (KMU) im Land Bremen – genau das fördert der RegioInnoGrowth Fonds. Mit Hilfe von offenen und stillen Beteiligungen unterstützt die BAB innovative wachstumsorientierte Geschäftsmodelle.
Zur PressemitteilungWenn 6.500 Mikrofone auf eine Untertasse passen
Mikrosysteme sind allgegenwärtig – in aktuellen Smartphones arbeiten zum Beispiel mehr als zehn verschiedene Mikrosysteme, darunter Mikrofone, Gyroskope, Lautsprecher oder Beschleunigungssensoren. Die microfab Service GmbH ist eine der weltweit wenigen unabhängigen Herstellerinnen von diesen hochkomplexen Bauteilen – und will jetzt das Geschäft weiter ausbauen.
Zum ArtikelNeuer Geschäftsführer bei der BAB – Die Förderbank für Bremen und Bremerhaven
In der BAB – die Förderbank für Bremen und Bremerhaven fand zum 01.02.2025 ein Wechsel in der Geschäftsführung statt. Michael Lücken, der seit 2022 Teil der Geschäftsführung war, verabschiedet sich auf eigenen Wunsch aus der Doppelspitze. Sein Nachfolger, an der Seite von Ralf Stapp, ist Torsten Fischer.
Zur Pressemitteilung